Comparable steel grade
AISI | GB | DIN | JIS |
4140 | 42CrMo | 1.7225 | SMC440 |
Chemical composition (%)
Element | Content (%) |
Iron, Fe | 96.785 - 97.77 |
Chromium, Cr | 0.80 - 1.10 |
Manganese, Mn | 0.75 - 1.0 |
Carbon, C | 0.380 - 0.430 |
Silicon, Si | 0.15 - 0.30 |
Molybdenum, Mo | 0.15 - 0.25 |
Sulfur, S | 0.040 |
Phosphorous, P | 0.035 |
Mechanical Properties
Properties | Metric | Imperial |
Tensile strength | 655 MPa | 95000 psi |
Yield strength | 415 MPa | 60200 psi |
Bulk modulus (typical for steel) | 140 GPa | 20300 ksi |
Shear modulus (typical for steel) | 80 GPa | 11600 ksi |
Elastic modulus | 190-210 GPa | 27557-30458 ksi |
Poisson's ratio | 0.27-0.30 | 0.27-0.30 |
Elongation at break (in 50 mm) | 25.70% | 25.70% |
Hardness, Brinell | 197 | 197 |
Hardness, Knoop (converted from Brinell hardness) | 219 | 219 |
Hardness, Rockwell B (converted from Brinell hardness) | 92 | 92 |
Hardness, Rockwell C (converted from Brinell hardness. Value below normal HRC range, for comparison purposes only) | 13 | 13 |
Hardness, Vickers (converted from Brinell hardness) | 207 | 207 |
Machinability (based on AISI 1212 as 100 machinability) | 65 | 65 |
Thermal Treatments.
Annealing: 1550F (840C), hold 2 hours, slow cool 50F(30C)/hr. max. to 1200F (650C), then air or furnace cool. Hardness
BHN 185/200.
Stress Relieving:
Annealed Material: 1100-1300F (595-740C), hold 2 hrs, air cool.
Hardened Material: 50-100F (30-55C) below last tempering temperature, hold 2 hrs, air cool.
Straightening: Best done warm 400-800F (205-425C)
alloy steel bar 42CrMo Hardening: (Atmosphere or Vacuum Furnace)
alloy steel bar 42CrMo Preheat: 1250-1300F (675-705C), equalize
alloy steel bar 42CrMo High Heat: 1550-1600F (840-870C), soak 10 to 30 minutes. For vacuum hardening, use the high side of the high heat
range and soak times.
Quench: Oil quench to hand warm, 150F (650C). Temper immediately. Water quenching from 1550F (840C) may be
used for simple shapes and larger sections. Note vacuum furnaces must have oil quench capability to achieve
comparable results.
Temper: Tempering at 400-1200F (205-650C) for 1 hour per inch (25mm) of thickness at temperature is recommended
(2 hrs min). Air cool to room temperature.
Welding
Medium carbon steel filler material.
Annealed Material:
alloy steel bar 42CrMo Preheat: 400F (205C)
Post heat: 500-600F (260-315C)
Hardened Material:
alloy steel bar 42CrMo Preheat: 50F (30C) less than last tempering temperature.
alloy steel bar 42CrMo Postheat: 50F (30C) less than last tempering temperature.
Production Equipment
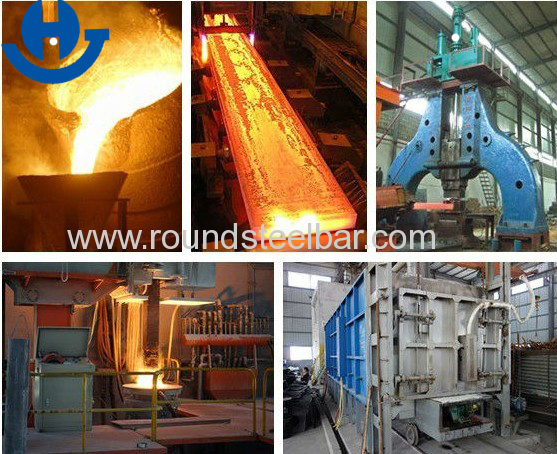
Processing Equipment
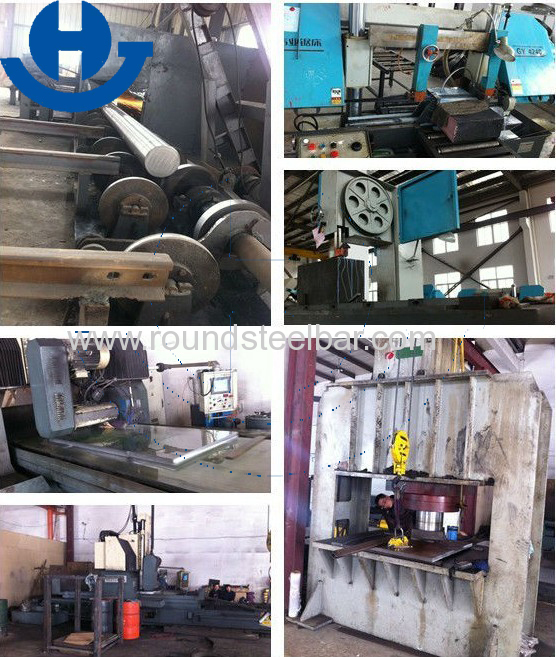
Black Steels

Peeling Steels
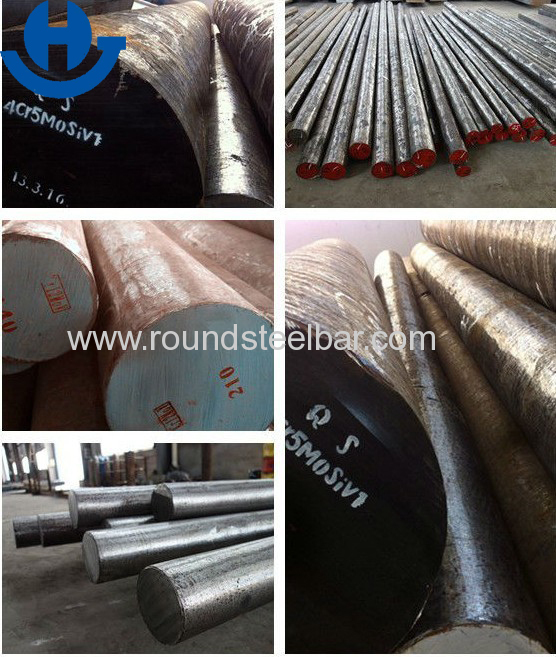
finished steel
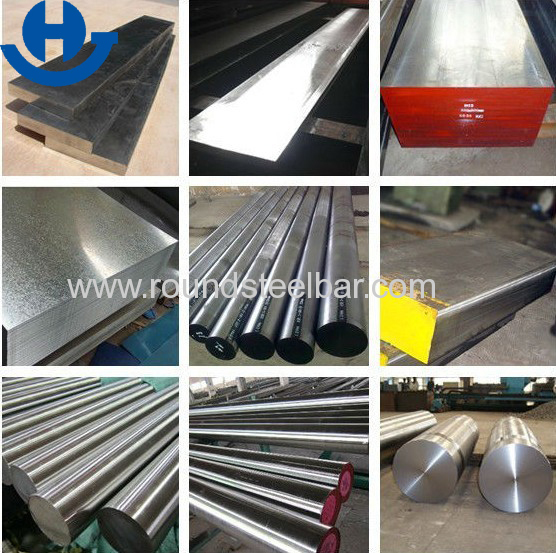
Testing Equipment
